UK-based Stratasys reseller Tri-Tech 3D has supplied aerospace design and manufacturing firm Airframe Designs with a second Fortus 450mc FDM 3D printer.
Having acquired its first Stratasys 3D printer back in 2020, the aerospace company has leveraged the 450mc to fabricate repeatable end-use parts as part of the National Aerospace Technology Exploitation Programme (NATEP). This £20 million, UK Government-funded project aims to develop and manufacture airworthy parts with water-soluble supports, to speed up production and reduce the potential for damage during post-processing.
The Stratasys 3D printer has also allowed Airframe Designs to manufacture customer parts, including tooling and assembly aids, with materials certified for aerospace applications.
The decision to acquire a second Fortus 450mc was driven by a need to scale up production and meet growing customer demand. For instance, the 3D printer has enabled the firm to successfully deliver an order for a complex 25-part assembly in just four working days.
“Now we have experience with the Fortus 450mc, we know with 95 percent confidence that it will build optimally,” commented Airframe Designs’ additive manufacturing manager Garry Sellick. “Typically we are achieving ±0.5 mm accuracy, which is the tolerance we work to, and we’re achieving a high level of repeatability. While we’ve had very few problems, we know Tri-Tech 3D is always on the end of the phone if we need something.”
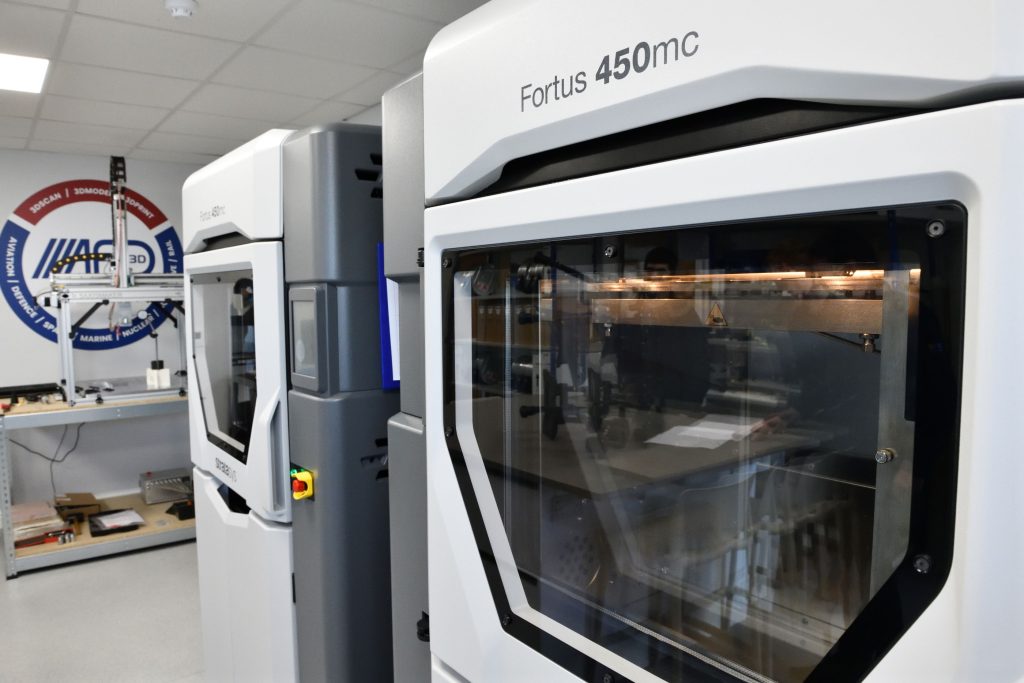
Airframe Designs purchases a second Fortus 450mc
Airframe Designs’ purchased its first Fortus 450mc from Tri-Tech 3D in July 2020, with the 3D printer initially split between the NATEP project and the production of customer parts. However, it soon reached full capacity, with the company unable to take on additional part orders. The delivery of the second 450mc has allowed the firm to increase its production capacity, and support more customer projects.
An industrial-scale FDM 3D printer, Stratasys’ Fortus 450mc features a large 406 x 355 x 406 mm build volume and is compatible with a range of high-performance materials including ABS, ASA, Nylon and ULTEM 9085. According to Stratasys, the 450mc offers the high repeatability and accuracy required for the production of aerospace-validated parts.
“With the Fortus 450mc, the team at Airframe Designs has been able to edit print parameters to optimize machine performance, a benefit for the NATEP programme and for its customers,” explained Robert Pitts, sales manager at Tri-Tech. “Available with a suite of validated materials, the Fortus 450mc is suitable for a wide range of aerospace applications, including cabin parts and tooling.”
Airframe Designs is not the only aerospace manufacturer to leverage the 450mc. In 2021 Senior Aerospace BWT, a UK-based manufacturer of air distribution systems for the aerospace sector, installed two of the FDM 3D printers at its Cheshire production site. The Stratasys technology has been utilized to enable in-house manufacturing of 3D printed interior aircraft parts for its customers.
Similarly, UK-based aircraft design and maintenance company Marshall Aerospace and Defence Group (ADG) has used the Fortus 450mc to produce tooling, prototypes, and functional parts for aircraft. The FDM 3D printer has reportedly allowed the company to meet increasingly aggressive deadlines and more complex manufacturing requirements.
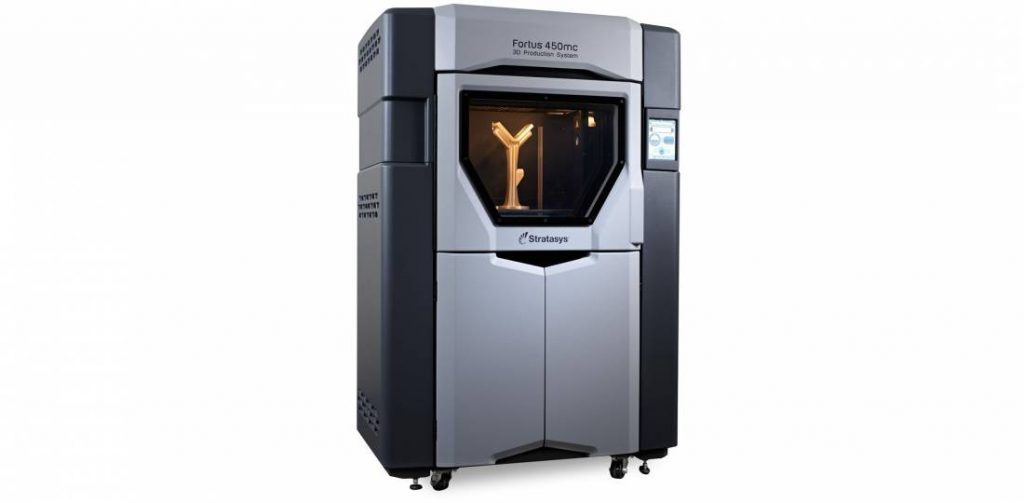
3D printing aerospace parts
The use of additive manufacturing is growing within the aerospace sector. Last year, 3D printing service bureau BEAMIT SpA announced that it was providing aerospace parts 3D printed in NASA-qualified AlSi7Mg aluminum for the production of Northrop Grumman-manufactured Cygnus spacecraft.
Produced using Laser Beam Powder Bed Fusion (LPBF), the 3D printed space rocket parts are NADCAP certified, reportedly exceeding NASA’s minimum material requirements.
More recently, GE Aerospace, the aerospace and aviation division of US energy multinational General Electric (GE), revealed plans to invest over $650 million into its global manufacturing plants and supply chain this year.
This will reportedly enable the firm to scale the production of its 3D printed Leap jet engines, which power the Airbus A320neo, Boeing 737 MAX, and COMAC C919 aircraft. The finances will also be used to enable the full-scale production of the GE9X engines, which feature over 300 3D printed parts.
Elsewhere, Los Angeles-based metal 3D printing specialists 3DEO announced a strategic partnership with aerospace engineering and manufacturing firm IHI AEROSPACE (IA). Through this partnership, IA hopes to increase its adoption and implementation of additive manufacturing by leveraging 3DEO’s expertise in Design for Additive Manufacturing (DfAM) and technology differentiation.
What does the future of 3D printing hold?
What near-term 3D printing trends have been highlighted by industry experts?
Subscribe to the 3D Printing Industry newsletter to keep up to date with the latest 3D printing news.
You can also follow us on Twitter, like our Facebook page, and subscribe to the 3D Printing Industry Youtube channel to access more exclusive content.
Are you interested in working in the additive manufacturing industry? Visit 3D Printing Jobs to view a selection of available roles and kickstart your career.
Featured image shows the Fortus 450mc FDM 3D printer from Stratasys. Photo via Tri-Tech.